Novel IHR OCXOs as Ultra-Stable Low-Power Frequency and Time References
Abstract. This article reviews recent achievement in development of the low power OCXO technology based on concept of internally heated resonators (IHR). The exhibited results prove that developed designs are perfect frequency control and timing solutions for a plenty of up-to-date electronic equipment especially with battery supply.
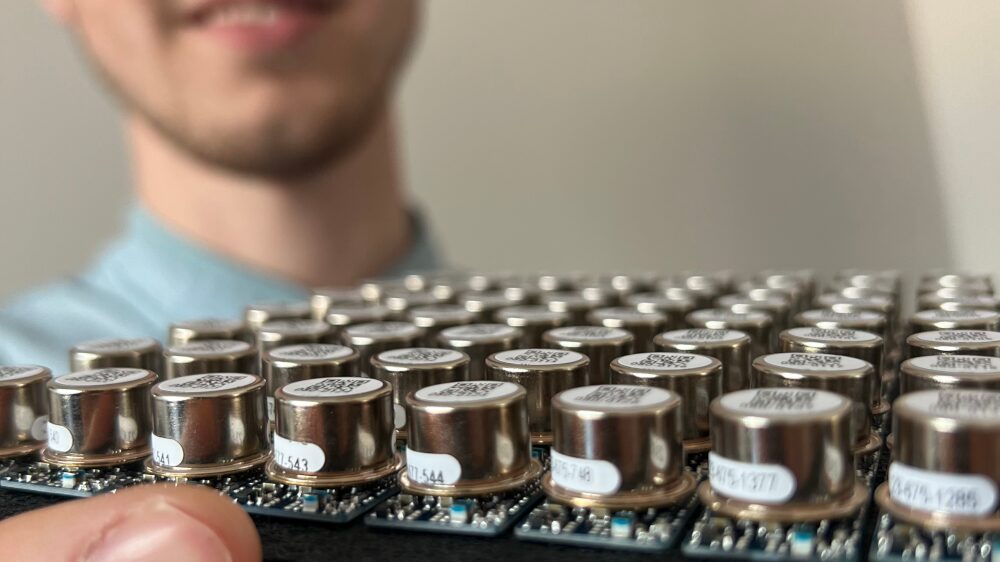
1. Introduction
High precision frequency references and master clocks are presently part and parcel of most professional radio-electronic equipment to a large extend determining its basic performances. For a plenty of modern applications, such as high-end portable radio and GPS, portative instrumentation, mobile radars and others, especially with battery supply, high frequency stability and timing accuracy of the reference should go along with its smallest sizes and lowest power consumption.
Nowadays these contradicting properties are successfully implemented at the chip scale atomic clocks/reference (CSAC) – miniature cesium oscillator with semiconductor laser stimulation and disciplined TCXO in the output.
The most advanced SA.65 model exhibits typical 1 ppb/month aging and 0.3 ppb stability within wide temperature range at 120 mW power consumption and 17 ccm packaging. These extraordinary performances make the CSAC excellent solution for high precision timing of various autonomous systems, operating in absence of GPS synchronization. The example is the equipment for underwater seismic geology exploration embedded in the sensor node disposed on sea bottom. The CSAC ensures precision timing of the reflected from the ground acoustic waves providing long operation time of the system between very expensive procedures of its recalibration and recharging the batteries on the surface.
Disadvantages of the CSACs are rather poor short-term stability and phase noise that along with substantial cost factor can restrict their usage in some modern projects.
As promising alternative to the CSACs, there can be considered the low power OCXOs using the internally heated resonators (IHR) technology. Owing to arrangement of the whole heating structure inside the vacuum crystal holder such devices provide much smaller sizes, power consumption and warm-up time than the conventional OCXOs. However, till recently the IHR oscillators had exhibited moderate long-term and temperature stability that restricted their application in high rank equipment.
This article reviews latest progress in the IHR technology making it perfect solution for a plenty of up-to-date applications which earlier admitted usage of only high-end conventional OCXOs or atomic clocks.
2. Construction of the Low Power IHR Oscillator.
Construction of the IHR oscillator consists of IHR unit mounted on unheated PC board bearing the rest of the oscillator circuitry.
Internal structure of the IHR packaged in the TO-8 vacuum holder is depicted in Figure 1. It comprises the crystal plate integrated in the TO-8 holder with internal heating systems arranged on the ceramic substrate which in turn is mounted on the thermo-isolated supporting structure. Heating of the crystal plate is effected mainly through the mounting clips with high thermal conductivity while minor part of the energy comes via the thermal radiation and vacuum conductivity.
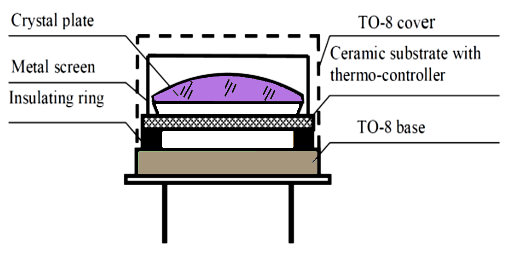
Very low thermal flows coming from the inner heated structure into environment due to its excellent thermal isolation ensures extremely low power consumption of the IHR oscillators, about one tenth of the conventional OCXO value. Besides, reduced thermal losses in the IHR result in low thermal gradients over the crystal plate that provides high accuracy of the operation crystal temperature at ambient temperature changes.
Absence of bulky oven structure being inherent in the conventional OCXO designs has allowed creation of miniature unpackaged DIP8 and DIP14 compatible models (XBO8, XBO14) and a bit larger XBO20S oscillator bearing more sophisticated electronic curcuitry ( Figure 2).
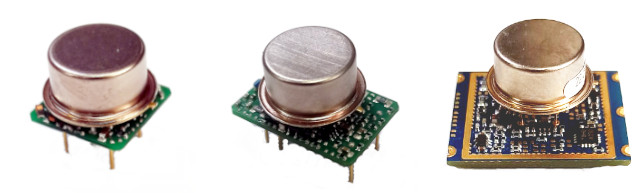
Table 1 indicates power consumption of these oscillators at 25 ºC for different ambient temperature ranges. Obviously the heating power falls almost linearly with decrease of upper ambient temperature due to appropriate lowering of the internal operation temperature. At narrow temperature ranges, it aporoaches 50 mW that seems extraordinary property for high stability OCXOs.
Temperature range, ºC | 0 +50 | -20 + 70 | -40 +85 |
Power consumption at 25ºC, mW | 45 | 65 | 90 |
3. Temperature Stability.
The unheated sustaining circuitry of the IHR oscillator is subjected to wide ambient temperature changes and therefore is the most substantial cause of the frequency vs. temperature instability. For a long time it was significant factor restricting application of these oscillators in high precision equipment.
The task of significant improvement of temperature stability of the IHR oscillators has been solved using additional compensation of the frequency error with digital or analog circuitry producing correction bias on the frequency corrector in accordance with ambient temperature changes (Figure 3).
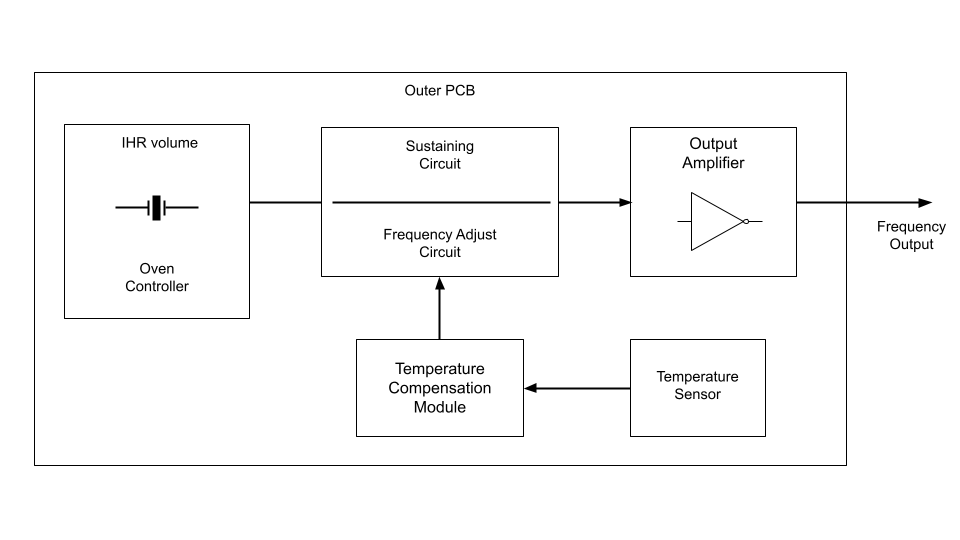
Table 2 displays temperature stability of the 10 MHz oscillators provided by the OCXO-temperature compensated (TC) technique in different temperature ranges.
Temperature range, ºC | 0 +50 | -20 + 70 | -40 +85 |
Frequency stability around 25ºC (typ), ppb | 0.2 | 0.3 | 0.4 |
Out of the data the stability of ±0.2ppb and ±0.4ppb are reached for (0 +50)ºC and (- 40 +85)ºC ranges respectively that approach the level of the most advanced conventional OCXOs.
4. Long-Term Stability (Aging)
Long-term instability or aging of crystal oscillators determines deviation of the frequency and error of the clocks over long period – days, months, years. This phenomenon is additive result of many physical processes in the crystal resonator:
- Relaxation of mechanical stresses in the crystal plate induced by the mounting structure.
- Molecular mass transfer inside the resonator vacuum volume.
- Changes of thermal gradients over the crystal plate of the IHR due to changes of vacuum conductivity in the resonator volume.
Reduction of initial mechanical forces from the mounting structure has demanded choice of appropriate material, form and number of the mounting clips. Usage of the stress-compensated SC-cut has ensured additional decrease of the forces influence on the IHR frequency.
Elimination of the molecular factors on the IHR aging has been achieved upon experimental study of complex sorbtion processes in the resonator volume during IHR manufacturing and operation. Based on the obtained physical model essential amendments in the resonator technology have been introduced, which includes usage of the low outgazing materials and special gettering substance, optimal vacuum cleaning before IHR sealing, training after packaging and some other measures.
Implementation of these amendments has led to the low aging technology of the IHR oscillators (LAT) bringing their long-term stability up to the level of compact size atomic clocks.
Figure 4 displays statistic of the aging rate of a group of 33 pcs the low aging IHR oscillators operating at 16.384 MHz.
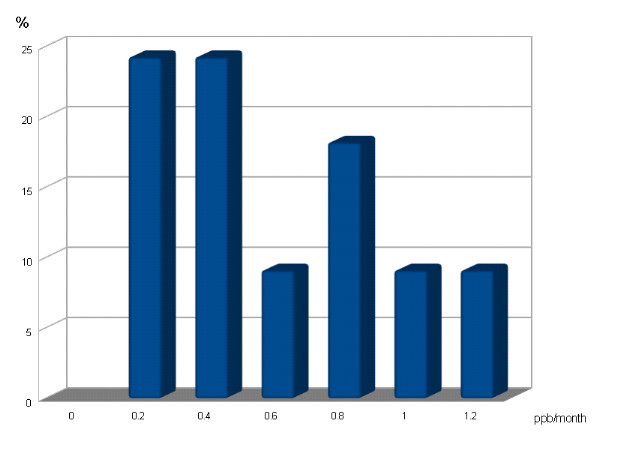
As one can see from the data about 90% of the tested units exhibit below 1 ppb per month aging rate after 30 days operation and 50% have 0.5 ppb per month.
Even better results have been obtained with the IHR oscillators operating at 10 MHz on the 5th overtone crystals. The Figure 5 depicts their aging during first 20 days of operation and calculated prediction for next month operation.
Out of the data for all the oscillators about 0.5 ppb/month rate is predicted after 20 days operation that even surpaces the stability of SA.65 atomic clock model.
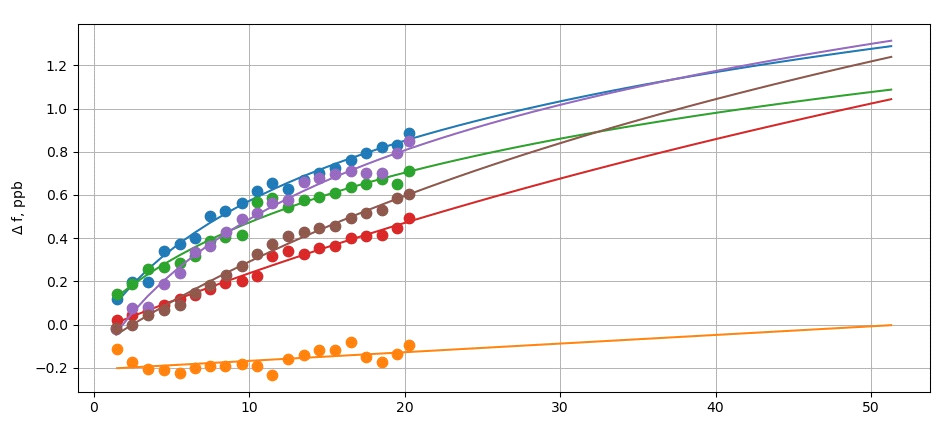
5. Phase Noise and Short-Term Stability (STS)
The phase-noise of crystal oscillator can be determined as random fluctuation of frequency or phase of the output signal. This parameter is of great importance for a number of modern radioelectronic systems, such as radars, radio transmitters, receivers, high speed data transmission and others.
In the IHR oscillators the phase-noise originates from the following internal factors:
- Inherent noise of the sustaining circuitry proceeding from fluctuation of the components parameters and thermal Jonson’s noise; its influence on the resonator phase-noise is restricted by loaded Q-factor of the resonator.
- Flicker noise of the resonator caused mainly by fluctuations of defects, contaminations or other fractions in the film electrodes or in the electrod- surfaces boundary.
- Temperature fluctuations in the IHR oven system impacting on the resonator frequency via its thermodynamic sensitivity.
Study of connection of these noise factors with the resonator and oscillator technology has allowed elaboration of the “low-noise techniques” enabling radical improvement of the IHR oscillators phase-noise performances to the level of the low-noise conventional OCXOs (Figures 6 and 7).
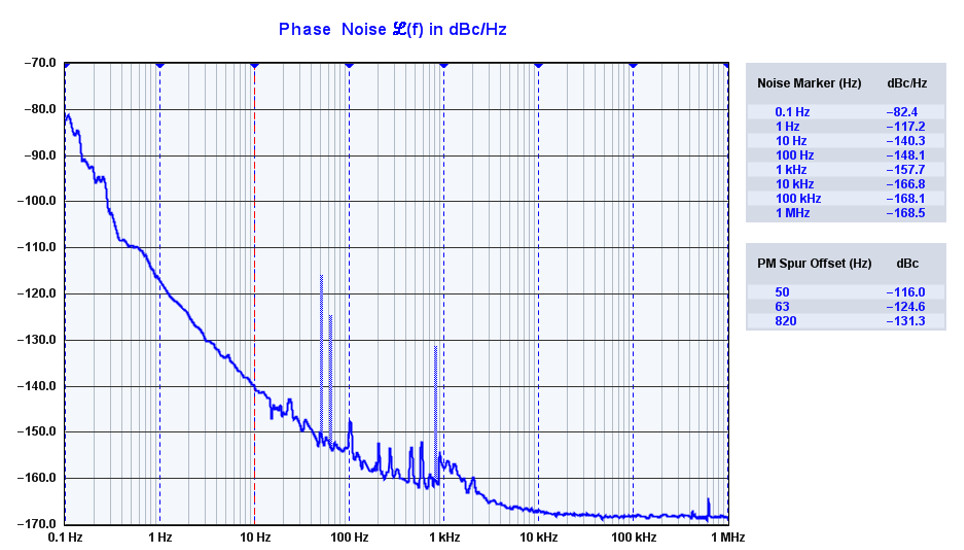
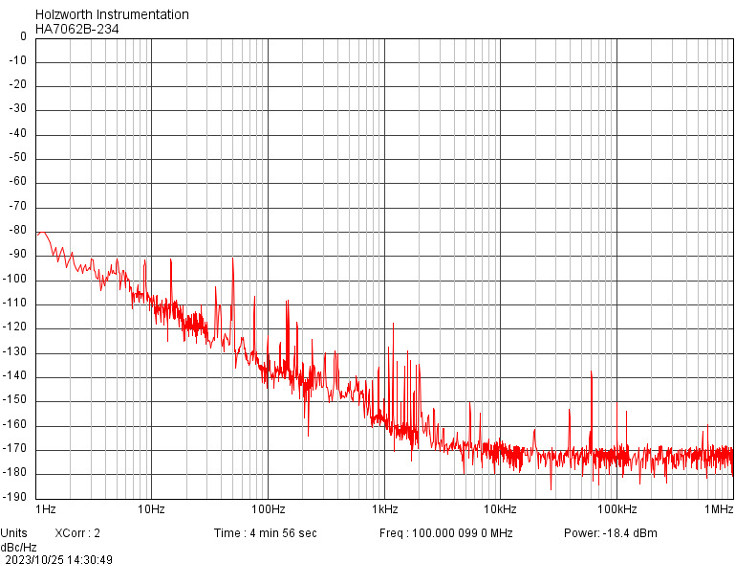
In the time domain the phase-noise parameters correlate with Allan deviation (AD) which depends also on the average time – period of the frequency measurement ranging normally from 1 ms to 1000 s. The Figure 8 depicts the AD of the low noise 10 MHz IHR oscillators. Out of the plot at 1 s average time the AD reaches 5E-13 that is excellent result even for the low-noise conventional OCXOs.
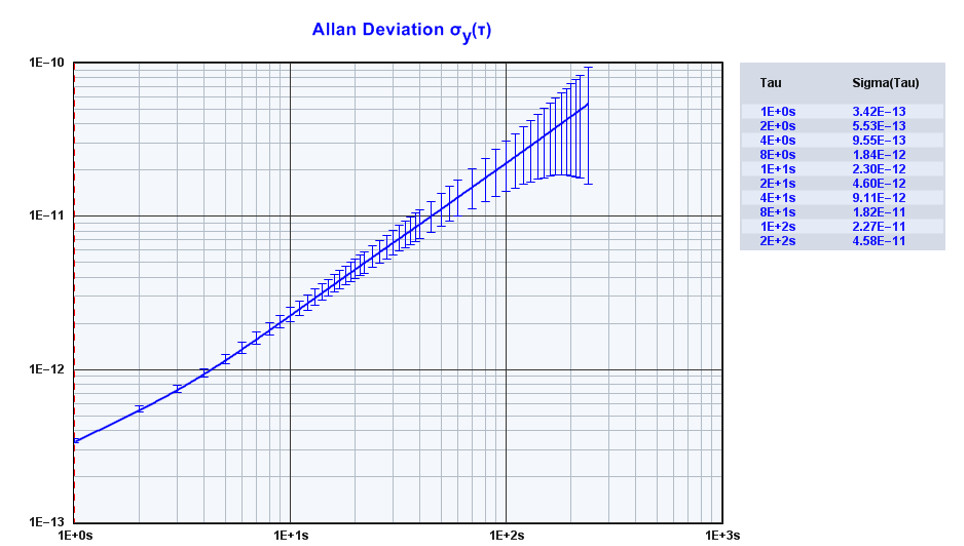
6. Acceleration Sensitivity.
Excellent phase-noise performances of the oscillators can be deteriorated noticeably if subjected to various mechanical factors, such as vibration, shocks, acoustic noise or acceleration, including gravitation field. These factors act on the resonator frequency via its acceleration sensitivity or g-sensitivity G coupling spectra of the acceleration amplitude A(Ω) with spectra of relative frequency deviation:
∆F/F(Ω )=A(Ω) * G
Value of the phase-noise degradation depends on distribution of the acceleration A(Ω) over effective frequency range Ω. For instance, sine vibration with amplitude A and frequency Ω causes phase-noise distortion at Ω offset from the operation frequency F at acceleration sensitivity G equaled to:
L( Ω) = 20 log [G*A( Ω)*F/2 Ω] (dBc/Hz)
Thus, reduction of influence of the mechanical factors on the oscillator frequency and its phase-noise requires minimization of g-sensitivity of the resonator. The g-sensitivity is a vector with 3 orthogonal components Гx, Гy, Гz usually coinciding with 3 main dimensions of the oscillator or of the resonator (Figure 9).
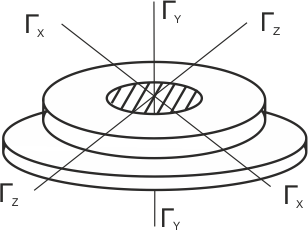
As it follows from carried out researches in-plane components of the g-sensitivity Гx, Гz originate from bending of the crystal mounting clips under in-plane forces Fx and Fz . The normal component Гy is caused by flexure of the plate under orthogonal force Fy. At flat plate Гy approaches zero, while at its plano-convex form it shows quite noticeable value.
In the novel IHR designs the acceleration sensitivity in all the 3 directions have been minimized using the following techniques:
- Anti-stress form of the mounting clips minimizing the thickness-shear loading on the plate from Ax and Az in-plane acceleration components.
- Increase of curvature radius of the convex plate for minimization of the normal Гy sensitivity. component.
- Application of stress-compensated SC-cut of the crystal.
Introduction of all these innovations has led to reduction of acceleration sensitivity of the XBO products to 0.2 ppb/g for “the worse” direction compared to 0.5 – 1 ppb/g typical value of the conventional OCXOs.
7. Comparison of the Novel IHR Oscillators with Advanced Conventional OCXOs and Chip-Scale Atomic Clocks.
Table 3 presents summary of basic performances of the most stable XBO20S model of Xtal Ball Technology in comparison with ultra-stable OCXO model AXIOM40/45HS of AXTAL GmbH and chip scale atomic clock SA.65 of Microchip Technology.
Basic performances | XBO20S (IHR OCXO) | AXIOM40/45HS (Conventional OCXO) | SA.65 (CSAC) |
---|---|---|---|
Stability in (-40 +80)ºC range, ppb | ±0.4 | ±0.1 | ±0.3 |
Aging per month (typ) after 30 days operation, ppb | 1 | 2 | 0.9 |
Allan deviation at 1s average time | 1E-12 | 5E-12 | 3E-10 |
Power consumption at 25ºC, mW | <100 | 750 | 120 |
Warm-up time to 0.1 ppm, min | <1 | <5 | – |
Volume, ccm | 8 | 16 | 17 |
Weight, gram | 8 | 25 | 35 |
Out of the data the XBO20S yields somewhat to AXIOM40/45HS model in the temperature stability having at that lower aging rate and better short-term stability at 1 s average time. The most striking advantages of the XBO20S over the conventional design are multiple lower power consumption, much smaller sizes and shorter warm-up time.
In comparison with the atomic SA.65 model the IHR oscillators exhibit similar temperature stability and aging rate at about 20% lower consumption, smaller sizes and drastically better short-term stability.
8. Application Fields
Extraordinary performances of XBO8, XBO14, XBO20 oscillators make them universal frequency control and timing solutions for a wide range of modern applications. Owing to combination of high frequency stability and low phase-noise level with miniature sizes and exeptionally low power consumption the DIP8 and DIP14 compatible XBO8 and XBO14 models are perfect frequency reference for high-end portable radio, GPS, mobile radars, other equipment, especially with battery supply.
The ultra stable XBO20S oscillators can serve as secondary frequency standard in portable instrumentation, test equipment, STRATUM 2 system and other applications needing excellent holdover in absence of GPS synchronization.
Moreover, the XBO oscillators should be prospective for application in battery fed rescue (COSPASS-SARSAT) beacons as providing high quality radio- transmission at long time of the battery service.
One the most prospective fields for XBO application is underwater sensor nods used at the oil seismic exploration. Utmost frequency stability at lowest power consumption determine high accuracy timing of the geological data at long periods of underwater exploitation between the battery recharge. In this domain the IHR oscillators can successfully compete with CSACs as providing superior stability at lower power consumption, smaller sizes and substantially lower cost factor.